Analysis service center is one of the most important organizational parts of the company in which we invested enormous efforts, which was recognized by our customers. Through constant improvement and regular attendance of our service engineers in master courses at the inoprincipal, our service center continues to advance.
Fast and high quality service support of our field service engineers is an imperative for us.
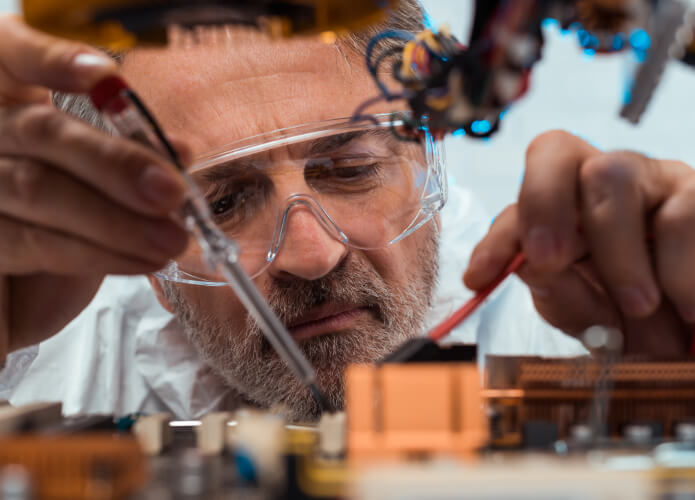
About the service center
With the increase in the number of our users, and our greater presence in the market, we have recognized the increasing need for adequate service and application support. Therefore, ANALYSIS DOO founded its service center as an independent organizational unit, registered under the full name ANALYSIS DOO Belgrade branch service center, whose task is technical and applicative client support, equipment care, which includes expert and timely maintemaintenance as well as service interventions in the case of unforeseen events.
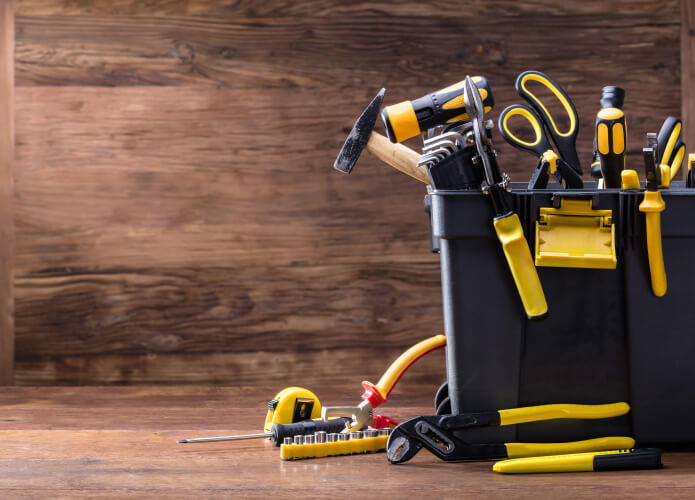
ANALYSIS owns their own vehicle fleet, which ensures on-time equipment delivery and reponse to the user’s requests, with respect to predetermined deadlines. Therefore we can guarantee fast and high quality servicing support in Serbia and the region, depending on our commercial program (Montenegro, North Macedonia, Bosnia and Herzegovina, Slovenia, Croatia and Albania).
The analysis team for servicing and applications currently hase more than fifteen highly qualified memebers. Our service engineers constantly improve their skills and knowledge, and we aim to offer adequate support for our users. All service engineers are certified by our equipment manufacturers and most of them have experience not only with servicing, but also working with different instruments and analytical techniques. Our service operaters have their own technical equipment.
If possible, the servicing can also be held online, which shortens the response time and reduces the costs of the servicing request.
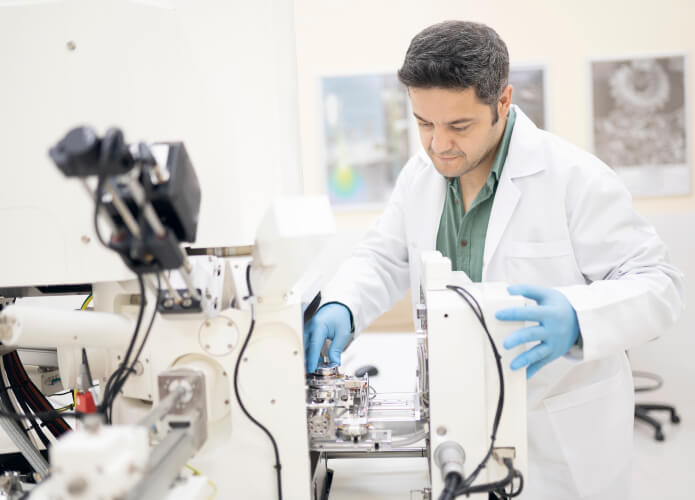
Service support and aims of the service centre
The installation of a new instrument and basic user are our standard services and are always included in the price of the device. Moreover, the installation and service support within the waranty period, as well as outside of it are available for the whole equipment assortiment.
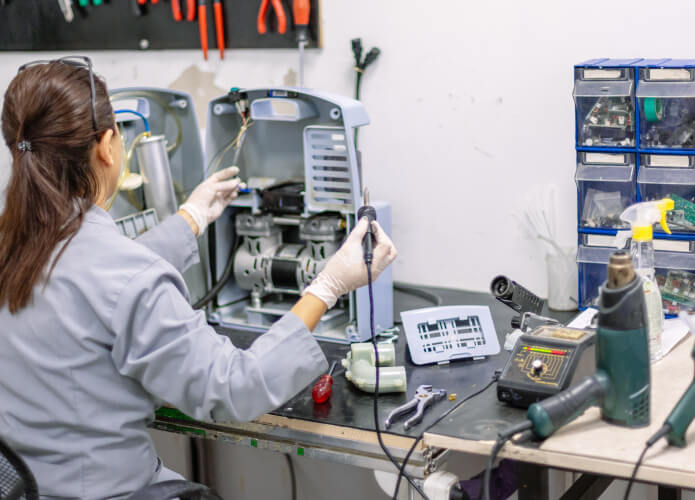
During the installation, equipment qualification is also performed, which is a standard procedure in the pharmaceutical industry, and more often in other types of labs. Equipment qualification has to be performed in the prescribed time interval. The basis of this approach are installational, operational and performance qualification protocols (IQ, OQ i PQ, respectively) which define all instrument checks, with the goal of guaranteeing the validity of the results, safety, and smooth operation. Our service engineers are certified to implement these protocols, as well as generate necessary documentation, by the manufacturer. If it is necessary, the documentation can also be generated in the electronic form, for systems combined in the form of LIMS (eng. Laboratory Information Management Systems), CDS (eng. Chromatography Data Systems), or similar.
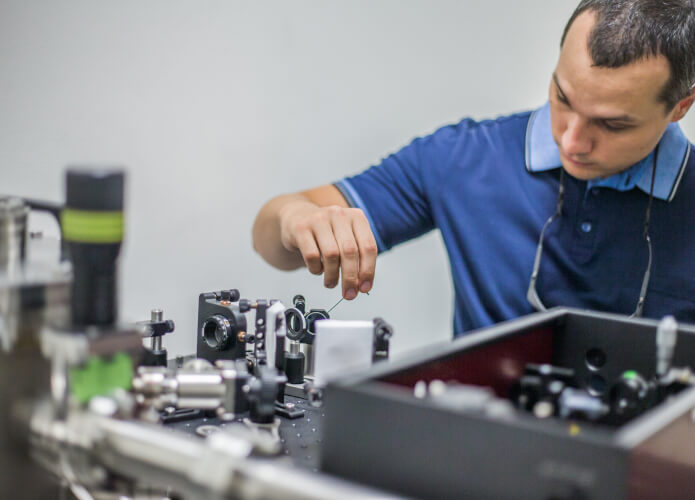
Devices that undergo regular maintenance do no, in the majority of cases, malfunction, and also this allows te user to be confident in their work, safety, as well as the results of the analysis. By following world trends, ANALYSIS introduced the concept of preventive and predictive maintenance. Preventive maintenance is planned ahead and performed in set time intervals, depending on the work load of the device. The aim of this maintenance is to prevent device malfunctions due to worn out parts, which therefore enables continuous operation. Predictive maintenance is the so-called smart equipment maintenance, where parts/consumables are exchanged depending on signs of wear, and exploitation period. This way, in contrast to preventive servicing, service costs are reduced, and generating unnecessary waste in the form of partially used spare parts is avoided.
In addition, as a special benefit, we offer contract servicing, which enable complete comfort of the user, continuous operation, and maximum productivity.